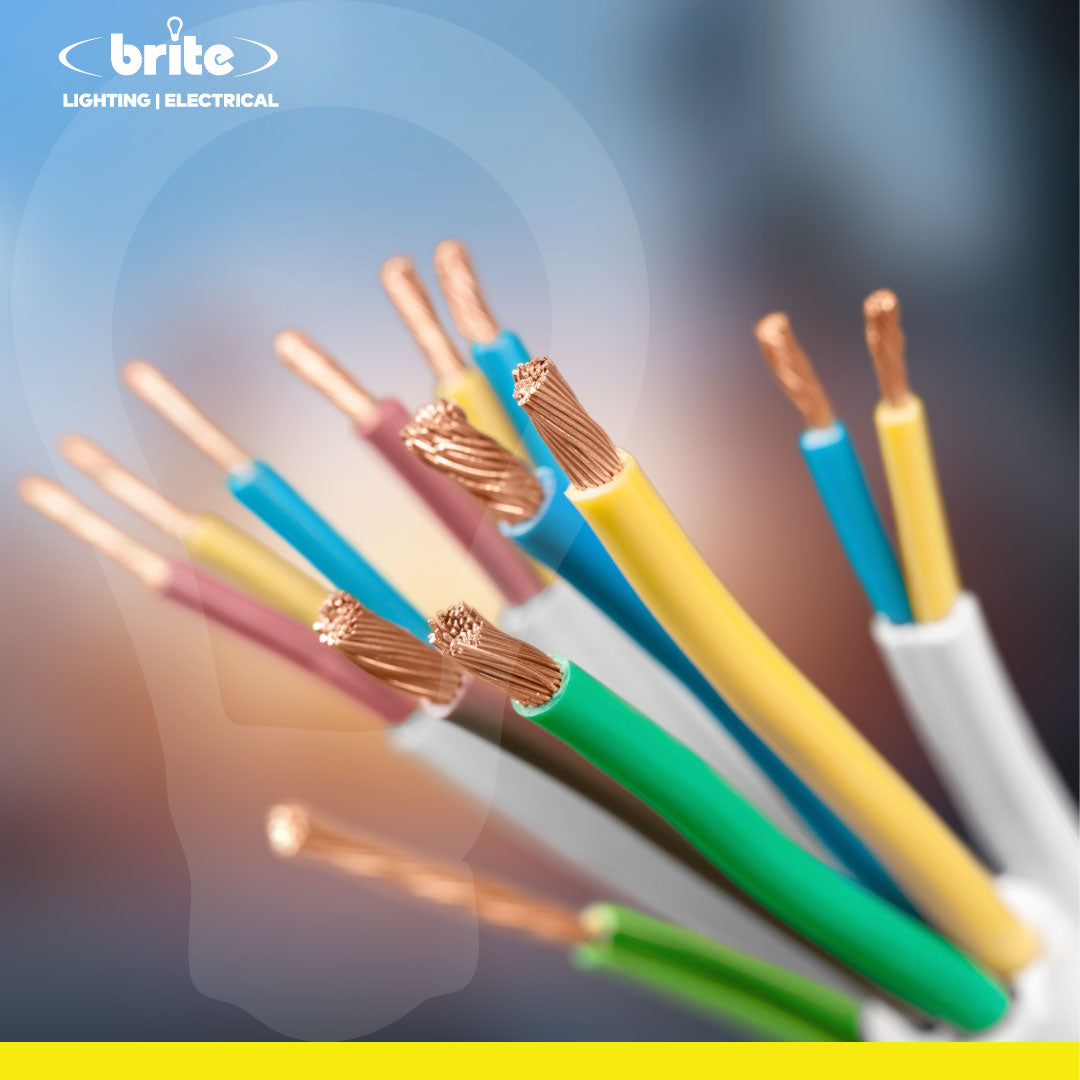
Your Guide to Electrical Cable Types & Their Applications
In the dynamic world of electrical installations, choosing the right type of electrical cable is crucial for ensuring safety, efficiency, and compliance with regulations.
This article aims to provide a comprehensive overview of different electrical cable types, their characteristics, and common uses.
Types of Electrical Cables:
Flat cable
A flat electrical cable, also known as flat twin and earth cable or flat twin flex, is a type of electrical cable that has a flat, ribbon-like shape. It is typically made of two or more insulated copper conductors that are laid up parallel and then encased in a flat PVC sheath. The cables may also include a separate insulated earth conductor for grounding purposes.
Flat electrical cables are commonly used for domestic and industrial wiring applications, such as:
- Under-plaster wiring: Flat electrical cables are often used for under-plaster wiring, where they are run through walls and ceilings. Their flat shape makes them easy to hide and less likely to damage the plaster.
- Surface wiring: Flat electrical cables can also be used for surface wiring, where they are run along the surface of walls and ceilings. Their flat shape makes them less obtrusive than round cables.
- Appliance wiring: Flat electrical cables are also commonly used for appliance wiring, such as connecting ovens, stoves, and other appliances to the mains supply.
- Low-voltage applications: Flat electrical cables can also be used for low-voltage applications, such as connecting LEDs, security systems, and audio/video equipment.
Advantages of Flat Electrical Cables
Flat electrical cables offer several advantages over round cables, including:
- Easier to install: Flat electrical cables are easier to install than round cables, as they can be run through tight spaces and are less likely to snag or get tangled.
- Less obtrusive: Flat electrical cables are less obtrusive than round cables, as they can be more easily hidden.
- More flexible: Flat electrical cables are more flexible than round cables, making them easier to bend and run around corners.
Disadvantages of Flat Electrical Cables
Flat electrical cables also have some disadvantages, including:
- Lower current carrying capacity: Flat electrical cables typically have a lower current carrying capacity than round cables of the same size.
- More susceptible to damage: Flat electrical cables are more susceptible to damage than round cables, as they can be easily pierced or cut.
Choosing the Right Flat Electrical Cable
When choosing a flat electrical cable, it is important to consider the following factors:
- Application: The application of the cable will determine the type of cable that is needed. For example, a cable with a higher current carrying capacity is needed for an appliance that draws a lot of current, such as an oven.
- Conductor size: The conductor size of the cable must be large enough to handle the current that will flow through it.
- Voltage rating: The voltage rating of the cable must be high enough to handle the voltage that will be applied to it.
- Insulation type: The insulation type of the cable must be suitable for the environment in which it will be installed.
- Length: The length of the cable must be long enough to reach the desired destination.
It is always a good idea to consult with an electrical expert to choose the right flat electrical cable for your specific application.
Surfix Cable
Surfix cable is a type of electrical cable that is commonly used for surface wiring in residential and commercial buildings. It is a flat, ribbon-like cable that is typically made of two or more insulated copper conductors that are laid up parallel and then encased in a flat PVC sheath. The cables may also include a separate insulated earth conductor for grounding purposes.
Surfix cable is available in a variety of sizes and colours, and it is designed to be easy to install and maintain. It is also a relatively inexpensive type of cable, making it a popular choice for many applications.
Here are some of the key features of Surfix cable:
- Flat, ribbon-like shape: This makes the cable easy to install and hide, and it also makes it less likely to damage walls and ceilings.
- Multiple insulated conductors: This allows the cable to carry multiple circuits, which can reduce the number of cables that need to be installed.
- Separate insulated earth conductor: This ensures that the cable is properly grounded, which can help to protect against electrical shock.
- PVC sheath: This protects the conductors from damage and moisture.
Here are some of the applications of Surfix cable:
- Surface wiring: Surfix cable is commonly used for surface wiring, where it runs along the surface of walls and ceilings.
- Under-plaster wiring: Surfix cable can also be used for under-plaster wiring, where it is run through walls and ceilings.
- Appliance wiring: Surfix cable is often used for appliance wiring, such as connecting ovens, stoves, and other appliances to the mains supply.
- Low-voltage applications: Surfix cable can also be used for low-voltage applications, such as connecting LEDs, security systems, and audio/video equipment.
Here are some of the advantages of Surfix cable:
- Easy to install: Surfix cable is easy to install, as it can be run through tight spaces and is less likely to snag or get tangled.
- Less obtrusive: Surfix cable is less obtrusive than round cables, as it can be more easily hidden.
- More flexible: Surfix cable is more flexible than round cables, making it easier to bend and run around corners.
- Relatively inexpensive: Surfix cable is a relatively inexpensive type of cable, making it a popular choice for many applications.
Here are some of the disadvantages of Surfix cable:
- Lower current carrying capacity: Surfix cable typically has a lower current carrying capacity than round cables of the same size.
- More susceptible to damage: Surfix cable is more susceptible to damage than round cables, as it can be easily pierced or cut.
Choosing the Right Surfix Cable
When choosing Surfix cable, it is important to consider the following factors:
- Application: The application of the cable will determine the type of cable that is needed. For example, a cable with a higher current carrying capacity is needed for an appliance that draws a lot of current, such as an oven.
- Conductor size: The conductor size of the cable must be large enough to handle the current that will flow through it.
- Voltage rating: The voltage rating of the cable must be high enough to handle the voltage that will be applied to it.
- Insulation type: The insulation type of the cable must be suitable for the environment in which it will be installed.
- Length: The length of the cable must be long enough to reach the desired destination.
It is always a good idea to consult with a qualified electrician to choose the right Surfix cable for your specific application.
GP Wire
GP Wire, or general-purpose wire, is a type of electrical cable that is commonly used for residential and commercial wiring applications. It is a single-core or multi-core cable that is made of insulated copper conductors that are encased in a PVC sheath. The cables may also include a separate insulated earth conductor for grounding purposes.
GP wire is available in a variety of sizes and colours, and it is designed to be easy to install and maintain. It is also a relatively inexpensive type of cable, making it a popular choice for many applications.
Here are some of the key features of GP wire:
- Single-core or multi-core: GP wire can be single-core or multi-core. Single-core cables have a single conductor, while multi-core cables have two or more conductors.
- Insulated copper conductors: GP wire is made of insulated copper conductors. The insulation protects the conductors from damage and prevents electrical shock.
- PVC sheath: GP wire is encased in a PVC sheath. The PVC sheath protects the conductors from moisture and mechanical damage.
- Variety of sizes and colours: GP wire is available in a variety of sizes and colours. The size of the cable determines the amount of current that it can carry. The colour of the cable is often used to identify the circuit that it is part of.
Here are some of the applications of GP wire:
- Residential wiring: GP wire is commonly used for residential wiring, such as connecting light switches, outlets, and appliances to the mains supply.
- Commercial wiring: GP wire can also be used for commercial wiring, such as connecting power to offices, factories, and stores.
- Low-voltage applications: GP wire can also be used for low-voltage applications, such as connecting LEDs, security systems, and audio/video equipment.
Here are some of the advantages of GP wire:
- Easy to install: GP wire is easy to install, as it can be run through tight spaces and is less likely to snag or get tangled.
- Less obtrusive: GP wire is less obtrusive than round cables, as it can be more easily hidden.
- More flexible: GP wire is more flexible than round cables, making it easier to bend and run around corners.
- Relatively inexpensive: GP wire is a relatively inexpensive type of cable, making it a popular choice for many applications.
Here are some of the disadvantages of GP wire:
- Lower current carrying capacity: GP wire typically has a lower current carrying capacity than round cables of the same size.
- More susceptible to damage: GP wire is more susceptible to damage than round cables, as it can be easily pierced or cut.
Choosing the Right GP Wire
When choosing GP wire, it is important to consider the following factors:
- Application: The application of the cable will determine the type of cable that is needed. For example, a cable with a higher current carrying capacity is needed for an appliance that draws a lot of current, such as an oven.
- Conductor size: The conductor size of the cable must be large enough to handle the current that will flow through it.
- Voltage rating: The voltage rating of the cable must be high enough to handle the voltage that will be applied to it.
- Insulation type: The insulation type of the cable must be suitable for the environment in which it will be installed.
- Length: The length of the cable must be long enough to reach the desired destination.
It is always a good idea to consult with a qualified electrician to choose the right GP wire for your specific application.
Armour Cable
hAn armoured cable is a type of electrical cable that has a metal protective covering. The metal armour can be made of steel, aluminium, or lead. Armoured cables are used in a variety of applications where the cable needs to be protected from physical damage, such as underground or outdoor installations.
Why Use Armoured Cable
There are several reasons why you might choose to use armoured cable:
- Physical protection: Armoured cable is more resistant to physical damage than non-armoured cable. This makes it a good choice for applications where the cable is likely to be exposed to the elements, such as underground or outdoor installations.
- EMI/RFI shielding: Armoured cable can also provide some protection against electromagnetic interference (EMI) and radio frequency interference (RFI). This can be important for applications where the cable needs to be run near electrical equipment or radio antennas.
- Security: Armoured cable can also be used to deter theft or vandalism. The metal armour makes it more difficult to cut or damage the cable.
Types of Armored Cable
There are several types of armoured cable available, including:
- Steel tape armoured (STA) cable: STA cable is a type of armoured cable that has a steel tape armour. The steel tape is wrapped around the cable and then covered with a PVC sheath.
- Steel wire armoured (SWA) cable: SWA cable is a type of armoured cable that has steel wire armour. The steel wire is wrapped around the cable and then covered with a PVC sheath.
- Lead-covered cable: Lead-covered cable is a type of armoured cable that has a lead sheath. The lead sheath protects the conductors from moisture and corrosion.
Applications of Armored Cable
Armoured cable is used in a variety of applications, including:
- Underground power distribution: Armoured cable is commonly used for underground power distribution. The metal armour protects the cable from damage by rocks, tree roots, and other underground hazards.
- Outdoor power distribution: Armoured cable can also be used for outdoor power distribution. The metal armour protects the cable from damage by wind, rain, and snow.
- Control cables: Armoured cable can also be used for control cables. The metal armour protects the cable from EMI/RFI interference.
- Security cables: Armoured cable can also be used for security cables. The metal armour makes it more difficult to cut or damage the cable.
Choosing the Right Armored Cable
When choosing armoured cable, it is important to consider the following factors:
- Application: The application of the cable will determine the type of cable that is needed. For example, a cable with a higher current carrying capacity is needed for an application that draws a lot of current.
- Conductor size: The conductor size of the cable must be large enough to handle the current that will flow through it.
- Voltage rating: The voltage rating of the cable must be high enough to handle the voltage that will be applied to it.
- Armour type: The type of armour must be suitable for the environment in which the cable will be installed. For example, lead-covered cable is a good choice for applications where the cable is likely to be exposed to moisture.
- Length: The length of the cable must be long enough to reach the desired destination.
It is always a good idea to consult with a qualified electrician to choose the right armoured cable for your specific application.
Submersible Cable
A submersible cable is a type of electrical cable that is designed to be used in underwater environments. It is typically made of insulated copper or aluminium conductors that are encased in a watertight sheath. The cables may also include a separate insulated earth conductor for grounding purposes.
Submersible cables are used in a variety of applications, including:
- Submersible pumps: Submersible cables are used to power submersible pumps, which are pumps that are submerged in water to draw up water.
- Offshore oil and gas production: Submersible cables are used to power offshore oil and gas platforms.
- Underwater communications: Submersible cables are used to carry communications signals between underwater devices.
- Aquaculture: Submersible cables are used to power underwater aquaculture equipment.
Submersible cable design
Submersible cables are designed to withstand the harsh conditions of underwater environments. The sheath of a submersible cable is typically made of a material that is resistant to water, corrosion, and UV radiation. The conductors of a submersible cable are also insulated to prevent electrical shock.
Submersible cable applications
Submersible cables are used in a variety of applications, including:
- Submersible pumps: Submersible pumps are used to draw up water from wells, reservoirs, and other water sources. Submersible cables are used to power these pumps.
- Offshore oil and gas production: Offshore oil and gas platforms are used to extract oil and gas from underwater reservoirs. Submersible cables are used to power these platforms.
- Underwater communications: Submersible cables are used to carry communications signals between underwater devices, such as submarine communication cables.
- Aquaculture: Submersible cables are used to power underwater aquaculture equipment, such as fish tanks and feeding systems.
Features of submersible cable
- High-quality materials: Submersible cables are made from high-quality materials that are designed to withstand harsh underwater conditions.
- Watertight construction: Submersible cables are designed to be watertight, preventing water from entering the cable and damaging the conductors.
- UV protection: Submersible cables are often protected from UV radiation, which can damage the cable's insulation.
- Corrosion resistance: Submersible cables are made from materials that are resistant to corrosion, which can damage the cable's conductors and sheath.
- Flexibility: Submersible cables are flexible, making them easy to install and run through tight spaces.
- Durability: Submersible cables are durable and designed to last for many years.
Choosing the right submersible cable
When choosing a submersible cable, it is important to consider several factors, including:
- Application: The application of the cable will determine the type of cable that is needed. For example, a cable with a higher current carrying capacity is needed for a pump that draws a lot of current.
- Conductor size: The conductor size of the cable must be large enough to handle the current that will flow through it.
- Voltage rating: The voltage rating of the cable must be high enough to handle the voltage that will be applied to it.
- Sheath material: The sheath material of the cable must be suitable for the environment in which the cable will be installed. For example, a cable with a UV-resistant sheath is needed for an application where the cable will be exposed to sunlight.
- Length: The length of the cable must be long enough to reach the desired destination.
It is always a good idea to consult with a qualified electrician to choose the right submersible cable for your specific application.
Solar Cable
A solar cable, also known as a photovoltaic (PV) cable, is a type of electrical cable that is specifically designed for use in photovoltaic solar power systems. It is typically made of insulated copper or aluminium conductors that are encased in a watertight, UV-resistant sheath. The cables may also include a separate insulated earth conductor for grounding purposes.
Unlike traditional electrical cables, solar cables must be able to withstand the harsh conditions of outdoor environments. This includes exposure to sunlight, rain, snow, and extreme temperatures. As a result, solar cables are made from specially formulated materials that are resistant to these conditions.
Advantages of solar cables
- Durability: Solar cables are designed to be durable and withstand the harsh conditions of outdoor environments.
- Watertight: Solar cables are watertight to prevent water from entering the cable and damaging the conductors.
- UV resistant: Solar cables are UV resistant to protect them from the sun's harmful radiation.
- Corrosion-resistant: Solar cables are made from materials that are resistant to corrosion, which can damage the cable's conductors and sheath.
- Flexibility: Solar cables are flexible, making them easy to install and run through tight spaces.
- High electrical conductivity: Solar cables are made from high-quality conductors that have high electrical conductivity to minimise power loss.
- Long lifespan: Solar cables are designed to last for many years, matching the lifespan of solar panels.
Applications of solar cables
Solar cables are used in a variety of applications, including:
- Connecting solar panels: Solar cables are used to connect solar panels in series or parallel to form a solar array.
- Connecting solar panels to inverters: Solar cables are used to connect the solar array to the inverter, which converts the direct current (DC) electricity generated by the solar panels into alternating current (AC) electricity.
- Connecting solar panels to charge controllers: Solar cables are used to connect the solar array to the charge controller, which regulates the charging of solar batteries.
- Connecting solar panels to power distribution systems: Solar cables are used to connect the solar array to the power distribution system, which distributes the AC electricity generated by the solar array to the home or business.
Choosing the right solar cable
When choosing a solar cable, it is important to consider several factors, including:
- Application: The application of the cable will determine the type of cable that is needed. For example, a cable with a higher current carrying capacity is needed for an array that generates a lot of power.
- Conductor size: The conductor size of the cable must be large enough to handle the current that will flow through it.
- Voltage rating: The voltage rating of the cable must be high enough to handle the voltage that will be applied to it.
- Sheath material: The sheath material of the cable must be suitable for the environment in which the cable will be installed. For example, a cable with a UV-resistant sheath is needed for an application where the cable will be exposed to sunlight.
- Length: The length of the cable must be long enough to reach the desired destination.
It is always a good idea to consult with a qualified electrician to choose the right solar cable for your specific application.
Welding Cable
Welding cables are electrical cables used to connect a welding power source to an electrode. They are specially designed to withstand the high current and heat generated during welding. Welding cables are typically made of stranded copper or aluminium conductors that are encased in a flexible insulating jacket. The cables may also include a separate insulated earth conductor for grounding purposes.
Types of welding cables
There are three main types of welding cables:
- Primary welding cables: Primary welding cables are used to connect the welding power source to the welding transformer. They are typically made of large-diameter conductors to handle the high current flow.
- Secondary welding cables: Secondary welding cables are used to connect the welding transformer to the electrode holder. They are typically made of smaller-diameter conductors than primary cables.
- Grounding cables: Grounding cables are used to connect the welding power source to the ground. They are typically made of smaller-diameter conductors than primary or secondary cables.
Features of welding cables
Welding cables must have several important features, including:
- High current carrying capacity: Welding cables must be able to handle the high current flow generated during welding.
- Flexible: Welding cables must be flexible to allow the welder to move around freely.
- Heat resistant: Welding cables must be able to withstand the heat generated during welding.
- Durable: Welding cables must be durable to withstand the harsh conditions of the welding environment.
- Protective jacket: Welding cables must have a protective jacket to protect the conductors from damage.
Applications of welding cables
Welding cables are used in a variety of welding applications, including:
- Arc welding: Arc welding is the most common type of welding. It uses an electric arc to melt the metal to be welded.
- Gas welding: Gas welding uses a flame to melt the metal to be welded.
- Resistance welding: Resistance welding uses an electric current to heat and melt the metal to be welded.
Choosing the right welding cable
When choosing a welding cable, it is important to consider several factors, including:
- Application: The application of the cable will determine the type of cable that is needed. For example, a cable with a higher current carrying capacity is needed for an application that generates a lot of heat.
- Conductor size: The conductor size of the cable must be large enough to handle the current that will flow through it.
- Voltage rating: The voltage rating of the cable must be high enough to handle the voltage that will be applied to it.
- Insulation type: The insulation type of the cable must be suitable for the environment in which the cable will be installed. For example, a cable with heat-resistant insulation is needed for an application where the cable will be exposed to high temperatures.
- Length: The length of the cable must be long enough to reach the desired destination.
It is always a good idea to consult with a qualified electrician to choose the right welding cable for your specific application.
Silicone Cable
Silicone cables, also known as silicone rubber cables, are a type of electrical cable that is made with silicone rubber as the insulation material. Silicone rubber is a synthetic elastomer that is known for its high-temperature resistance, flexibility, and chemical resistance.
Silicone cables are commonly used in a variety of applications, including:
- High-temperature applications: Silicone cables are ideal for applications where the cable is exposed to high temperatures, such as in ovens, stoves, and other appliances. They can withstand temperatures up to 200°C (392°F).
- Flex applications: Silicone cables are also very flexible, making them well-suited for applications where the cable needs to be bent or moved frequently.
- Chemical-resistant applications: Silicone rubber is resistant to a wide range of chemicals, including acids, alkalis, and oils. This makes silicone cables a good choice for applications where the cable is exposed to harsh chemicals.
Silicone cables are made with stranded copper or aluminium conductors that are encased in a silicone rubber jacket. The jacket protects the conductors from damage and moisture. Silicone cables may also include a separate insulated earth conductor for grounding purposes.
There are several advantages to using silicone cables:
- High-temperature resistance: Silicone cables can withstand extreme temperatures up to 200°C (392°F).
- Flexibility: Silicone cables are very flexible, making them easy to install and use.
- Chemical resistance: Silicone rubber is resistant to a wide range of chemicals.
- Durability: Silicone cables are durable and can withstand harsh conditions.
- Electrical insulation: Silicone rubber is an excellent electrical insulator.
- UV resistance: Silicone rubber is resistant to UV radiation, making it suitable for outdoor applications.
- Long lifespan: Silicone cables have a long lifespan, typically 20 years or more.
There are a few disadvantages to using silicone cables:
- Higher cost: Silicone cables are more expensive than other types of electrical cables.
- Lower current carrying capacity: Silicone cables have a lower current carrying capacity than other types of electrical cables.
- Not as strong: Silicone rubber is not as strong as some other types of insulation materials.
When choosing a silicone cable, it is important to consider the following factors:
- Application: The application of the cable will determine the type of cable that is needed. For example, a cable with a higher current carrying capacity is needed for an application that draws a lot of current.
- Conductor size: The conductor size of the cable must be large enough to handle the current that will flow through it.
- Voltage rating: The voltage rating of the cable must be high enough to handle the voltage that will be applied to it.
- Insulation type: The insulation type of the cable must be suitable for the environment in which the cable will be installed.
- Length: The length of the cable must be long enough to reach the desired destination.
It is always a good idea to consult with a qualified electrician to choose the right silicone cable for your specific application.
Considerations When Choosing Electrical Cables:
- Voltage Rating: Ensure the cable's voltage rating matches the requirements of the electrical system.
- Conductor Material: Copper and aluminium are common conductor materials. Copper is known for its conductivity, while aluminium is often used in larger installations due to its cost-effectiveness.
- Insulation Material: Different applications require specific insulation materials to withstand environmental conditions, temperature variations, and potential exposure to chemicals.
- Cable Size and Ampacity: Selecting the right cable size is crucial for preventing overheating. Consider the ampacity requirements of the electrical system.
Installation and Maintenance Tips:
- Proper Installation: Follow manufacturer guidelines and industry standards for cable installation to ensure safety and performance.
- Regular Inspections: Periodic inspections can help identify signs of wear, damage, or potential issues, allowing for timely maintenance.
Conclusion on Electrical Cable Types & Applications
In the ever-evolving landscape of electrical installations, understanding the diverse types of electrical cables and their applications is essential. By considering factors such as voltage rating, conductor material, and insulation, one can make informed decisions to create safe and efficient electrical systems. Regular maintenance and adherence to regulatory standards further contribute to the longevity and reliability of electrical installations.